Efficient order fulfillment is essential for modern businesses striving to meet customer demands while minimizing costs and operational inefficiencies. NetSuite WMS (Warehouse Management System) is a powerful tool designed to streamline order fulfillment by optimizing inventory management, improving warehouse operations, and enhancing overall efficiency. In this blog, we’ll explore how NetSuite WMS helps businesses achieve these goals and why it’s a game-changer for order fulfillment.
Table of Contents
ToggleUnderstanding NetSuite WMS
NetSuite WMS is a cloud-based solution that integrates into NetSuite ERP to provide end-to-end visibility and control over warehouse operations. It allows businesses to automate workflows, improve inventory accuracy, and optimize processes like picking, packing, and shipping. It equips businesses of all sizes with real-time tracking, barcode scanning, and customizable picking strategies for better order fulfillment capabilities.
Features of NetSuite WMS That Optimize Order Fulfillment
Real-Time Inventory Management: The feature of NetSuite WMS gives real-time insights into the levels of inventory, thus giving a clear understanding of the stock availability at various locations. Businesses can track this stock level to avoid stockouts and overstocking, thus making order processing accurate.
Advanced Picking Strategies: NetSuite WMS supports wave picking, batch picking, and zone picking. These options would allow a business to choose which best fits their need to get orders processed more quickly and accurately.
Mobile Access: Mobile access will allow warehouse staff to do their work in the picking, packing, and updating of inventory on their mobile. This means no more paperwork and direct update of the system in real time, thus reducing errors and making it more efficient.
Integration with Barcode and RFID Technology: NetSuite WMS is equipped with seamless integration with barcode readers and RFID technology. These make it easier to track your inventory and reduce the possible errors in manual data input, thus making order fulfillment faster and more accurate.
Seamless ERP integration: The WMS module of the NetSuite Network integrates seamlessly with the ERP module. This allows for ease of communication between departments, from sales, to inventory management, and provides for a unified system in its end-to-end order fulfillment process.
Common Issues in Order Fulfillment: Order fulfillment often involves complexities that may erode the efficiency and quality of customer satisfaction. NetSuite WMS solves these problems easily
Inventory Inaccuracies
Back-hand storing or weakly integrated systems often lead to inventory mistakes that can result in stockouts or late orders. Data is real time, and with centralized management of the inventory, NetSuite WMS eradicates errors and ensures that a stock available.
The traditional way of picking time-consuming and prone to mistakes, NetSuite WMS supports higher strategies that expedite and save more time in decreasing the rate of mistakes in the picking process.
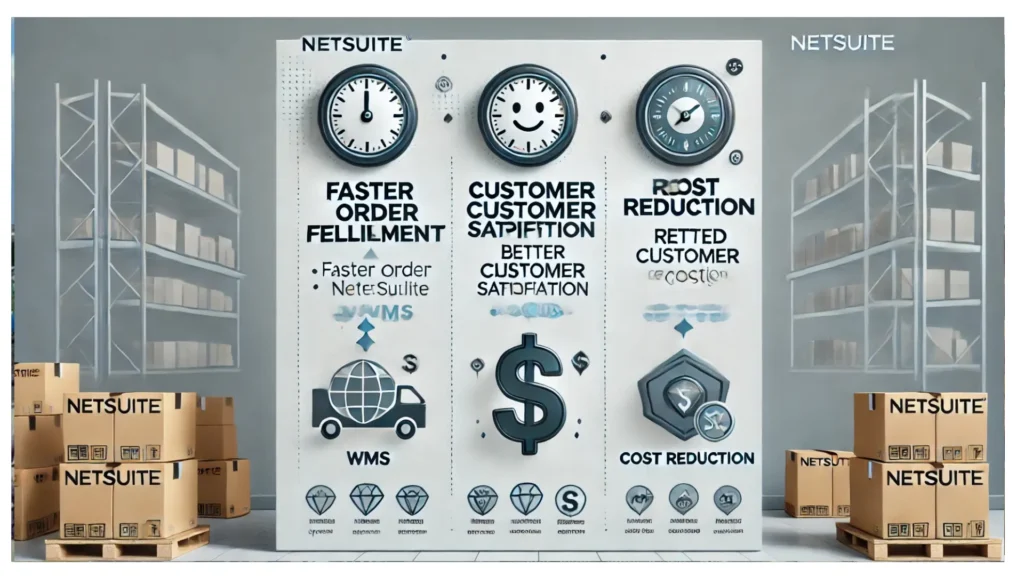
Lack of Real-Time Updates
Where communication is very low in systems leading to slower order status and lower level inventory. With NetSuite WMS, stakeholders gain timely data exchange as regards information into their operations.
Without automation, the businesses pay a higher wage bill and are prone to errors. NetSuite WMS automatically facilitates key processes, decreases dependency on manual effort and reduces operational costs significantly.
Benefits of NetSuite WMS in Order Fulfillment
Faster Order Fulfillment: Using NetSuite WMS, faster order fulfillment is possible through optimized picking, packing, and shipping mechanisms, that ascertain speed and reliability to the customer.
Some of the features of real-time barcode scanning and inventory updates significantly reduce errors so that the right product is delivered to the customer.
Better Customer Satisfaction: Orders are filled promptly and correctly, which makes for good experiences by customers, so loyalty and repeat business are ensured.
Operational Cost Reduction: Automation and workflow using less labor and lesser error rates reduce the operational costs of the business.
Scalability and Flexibility: The product is tailored to grow with the business, ideal for companies scaling operations without losing efficiency.
Steps to Implement NetSuite WMS
Implementing NetSuite WMS requires strategic approaches since the transition should be smooth and maximum benefits realized. Here’s a step-by-step guide:
Step 1: Assess Current Operations: First and foremost, benchmark your existing warehousing operations to spot the areas of pain and opportunity for improvements. The methodology will be adapted to the clients’ needs.
Step 2: Configuration of the System: NetSuite WMS will have to be adapted according to the business process of your company. This might include configuring picking strategies, integrating with barcode systems, configuration of inventory tracking parameters among others.
Step 3: Train Your Team: Warehouse staff and other stakeholders should receive comprehensive training. Knowing all the features and functionalities of the system would be pretty crucial to its successful implementation.
Step 4: Monitor Performance: After deploying the system, it will be a good practice to continue monitoring its performance so as to understand what can be optimized further. NetSuite offers reporting tools that are useful for tracking key metrics such as order accuracy and processing time.
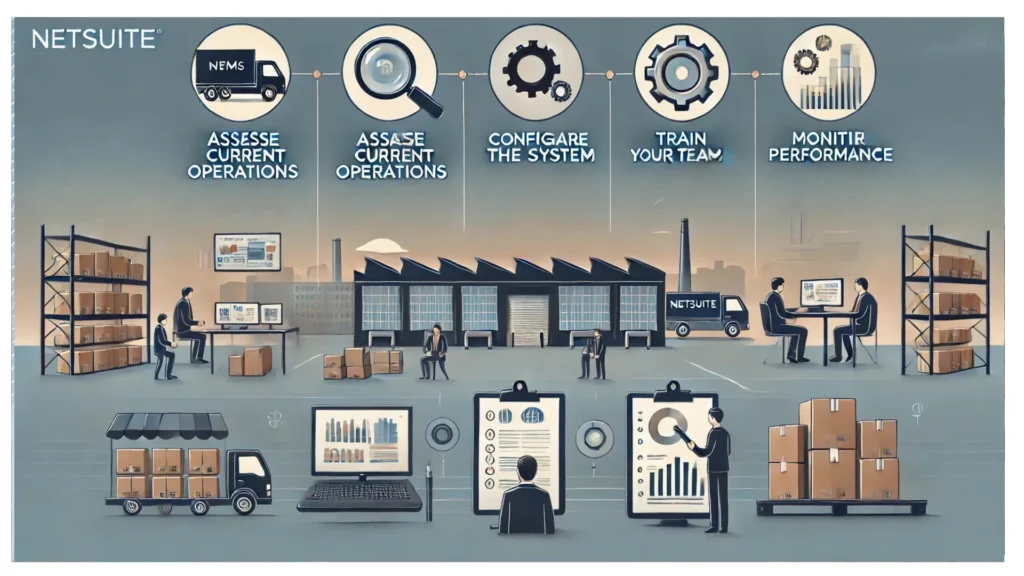
Case Study: Implementing NetSuite WMS
E-Commerce Retailer
An e-commerce retailer was taking too much time to process orders and was miscounting its inventory, which further frustrated its customers. After implementing NetSuite WMS, the company could enjoy the following:
- Reduction in order processing times by 40%
- Decreased error rate in picking by 30%
- Inventory in view through proactive replenishment stock
This brought the company operational efficiency along with customer satisfaction and loyalty.
Advanced Tips for Optimization of NetSuite WMS
Leverage real-time dashboards, use system dashboards to monitor critical metrics, such as order accuracy, warehouse productivity, and inventory turnover, to look at areas of continuous improvement.
Optimize picking strategies
Analyze various strategies in picking based on order volumes and warehouse layouts. Some may be appropriate for use in high volume orders with wave picking, and others may be better suited for larger warehouses that can utilize zone picking.
Update the System Routinely Maintain NetSuite WMS current regarding the latest features and integrations. This keeps the system aligned with your business evolution.
Integrate with Shipping Solutions: NetSuite WMS integration with the shipping carrier helps in smooth dispatch and real-time tracking of shipment, which again would increase customer satisfaction.
Order Fulfillment Using NetSuite WMS: Further adaptation by businesses in responding to the dynamic needs of their customers will continue to involve technologies such as AI and machine learning. Predictive analytics, automated inventory replenishment, and even more intelligent picking algorithms will become an integral part of order fulfillment in the future. NetSuite WMS adoption today puts businesses ahead of these changes as they come online.
Conclusion
Order fulfillment is a prime component of supply chain success, both in terms of customer satisfaction and business profitability. NetSuite WMS offers its users the right tools to handle their warehouse operations, reduce errors, and meet customers’ expectations. From real-time inventory tracking to advanced picking strategies, the system is an all-inclusive package to optimize order fulfillment.
This helps companies achieve operational excellence, scale up efficiently, and maintain a competitive edge in the market by implementing NetSuite WMS. Such an investment in the most recent innovation today would lead companies towards long-term success and resilience into meeting future challenges within the complex environment of logistics and supply chain management.